剪切测试
剪切盒
FT4同时还包含剪切盒附件,它可以量化粉体剪切特性(符合美国ASTM D7891)。剪切测试技术与动力学测试差别很大,通常用来表征处于固结状态的粉体。同时也是一种相对静态的测试,测量由非流动向流动状态转变时的粉体行为。
显而易见,正因为这些原因,对于呈固结状态、流动速率低和(或)流动时有时无的粉体,剪切盒非常适用于预测它们在加工操作中的表现。剪切盒已被成功用于认识料斗中的粉体行为,并为料斗设计工作提供了一些必要的数据(基于上世纪研究得出的Jenike应力理论)。但是,这种操作方式也使得剪切盒不太适合用于预测低应力或动态应用条件下的粉体行为,如混料、填充、喂料和输送等。
工作原理
在速率极低时,对上层粉体施加剪切力(或水平方向的力),同时阻止与其相邻的低层粉体移动(反之亦然)。不断增加这一作用力,但不发生剪切面的相对运动,直到剪切力高到足以克服粉体剪切力为止。此时,粉体基体发生“屈服”,上层粉体与下层粉体之间产生相对滑动。
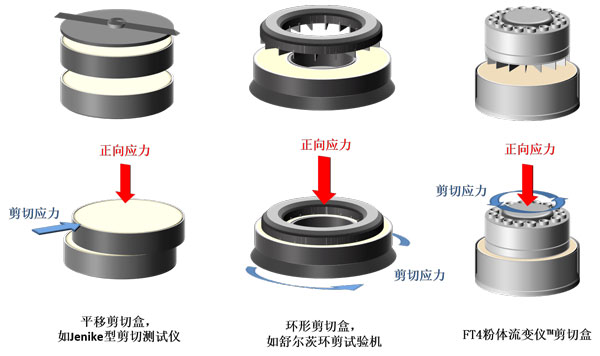
近50年来出现了几种剪切盒设计,然而采用的都是同一理念,即在粉体层之间进行相对剪切。目前最普遍的设计应用是旋转式的,它之所以得到青睐,是因为与很快就触及位移上限的传统设计相比,它可以使粉体的两层之间发生较大距离的相对剪切。
每一种设计都各有长短。所有设计目前都在使用。如需详细对照不同剪切方式的特点及优劣势,请直接联系我们获取更多信息。
按照常规的剪切盒测试程序,会在不同正向应力大小下进行几次剪切测试。获得的数据代表着剪切应力与正向应力之间的关系,可据此绘制确定粉体的屈服轨迹。简单来说,在一定的正向应力下,剪切应力越高,粉体越不可能屈服,当在料斗或其它容器中受到类似的固结应力时便会开始流动。
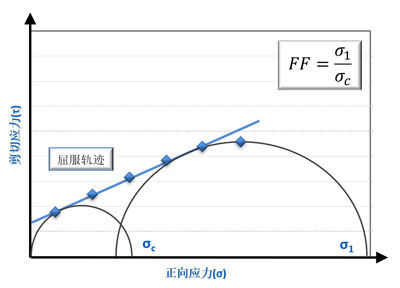
将多个数学模型应用于这一数据是可行的,但重要的是,应考虑到这样一来,趋势性可能被夸大或缩小。将莫尔应力圆与屈服轨迹进行拟合,可确定最大主应力(σ1)和无约束屈服强度(σc),前者与后者的比率即为流动函数值(FF)。流动函数是划分流动性等级的常用参数,其值低于4时意味着流动性差,高于10则表示流动性良好。
壁面摩擦
壁面摩擦测试提供了测量粉体与加工设备表面滑动摩擦的途径。这对于了解粉体从料斗中的出料行为、输送槽内的流动持续性和片剂脱模力尤为重要。同时,也有利于考察粉体是否会与加工设备壁面和其它各种表面如内袋、胶囊和其它包装材料发生粘连。
它的测量原理与剪切盒测试极为类似,但与粉体内的相对剪切不同,这一测试以代表加工设备器壁的材料试件与测试中的粉体进行相对剪切。FT4壁面摩擦附件可以对一系列试件进行考察,如果需要,可按照要求加工定制表面。
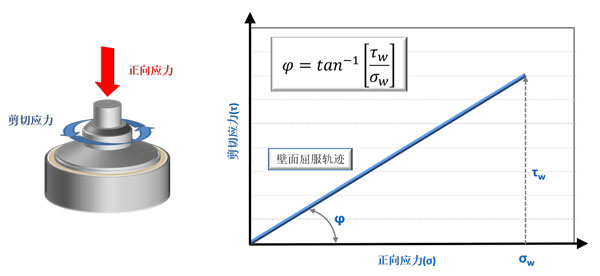
通常以剪切应力相对于正向应力的曲线来呈现数据,以便确定壁面摩擦角(φ)。壁面摩擦角越大,粉体与壁面试件间的阻力越高。
这一数据可用于上述示例等特定研究中,但也可作为料斗设计工作的一部分使用。
料斗设计
在整个加工环境中,料斗的使用十分广泛,虽然它们常被视为简单系统,实际却导致大量的加工中断和产品质量问题。
如果粉体所具有的特性没有针对料斗的形状和设备表面进行优化,那么,从料斗流出的速率就会波动,甚至根本流不出。但是,自从Andrew Jenike在20世纪中叶进行了前所未有的研究工作,如今人们已能够利用剪切盒和壁面摩擦测试中得到的数据,计算出能确保良好流动的关键料斗尺寸。
FT4配有全自动料斗设计软件,它直接采用来自剪切盒和壁面摩擦测试的结果数据,并通过料斗设计算法进行运算。不到3个小时,就可以完成全自动料斗设计。
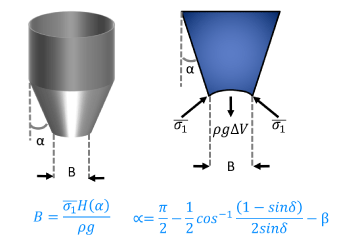
如今,这种基于对材料性质和设备内部应力机制的认知的料斗设计过程,依然是设备设计中极少数基本方法之一。不幸的是,对于混料器、喂料器、输送器、干燥器、压片过程或粉末加工中常用的其它常规作业单元,这种方式并不适用。
如需进一步了解料斗设计过程,请联系我们。
返回FT4页面